The Future of Plastic Shot Molding: Developments and patterns to View
As the plastic shot molding market develops, several vital patterns are emerging that assurance to reshape its landscape. Automation and smart production methods are set to boost efficiency, while the change in the direction of sustainable products shows an expanding environmental consciousness.
Automation and Smart Production
As the plastic shot molding industry evolves, automation and wise manufacturing are taking center phase, transforming manufacturing processes - Plastic Injection Molding. The assimilation of advanced technologies such as robotics, IoT (Internet of Things), and expert system is making it possible for suppliers to boost performance, reduce functional prices, and enhance item high quality. Automated systems simplify process, decreasing hands-on treatment and enhancing throughput, which is crucial in meeting the increasing need for rapid manufacturing cycles
Smart manufacturing innovations promote real-time monitoring and data evaluation, allowing business to maximize machine performance and anticipate upkeep needs. This positive strategy not just reduces downtime however additionally extends the lifespan of devices. The usage of joint robotics, or cobots, boosts the flexibility of production lines, enabling workers and devices to operate side by side safely and effectively.
The adoption of automation in plastic injection molding is not simply a pattern however a calculated imperative for businesses aiming to remain competitive in a global market. By harnessing these technologies, manufacturers can achieve greater accuracy, reduce waste, and adapt promptly to transforming client demands, positioning themselves for sustainable development in a significantly computerized future.
Lasting Materials and Practices
The push towards automation and clever production has led the way for a better focus on sustainable materials and techniques within the plastic shot molding market. Companies are increasingly looking for environment-friendly options to traditional petroleum-based plastics, leading to the fostering of bio-based and recycled materials. These lasting materials not only lower environmental impact yet likewise align with customer demand for greener items.
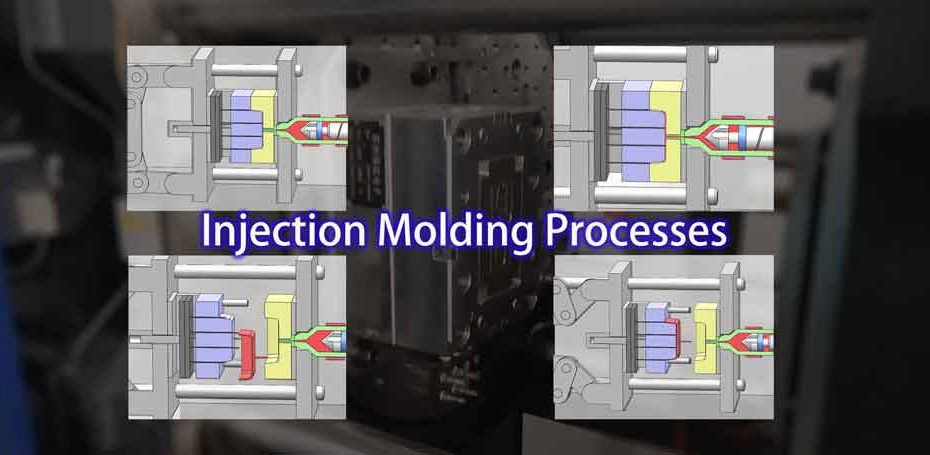
Moreover, partnership in between makers, product vendors, and ecological organizations is promoting development in the advancement of sustainable materials that fulfill efficiency criteria without endangering high quality. As guidelines around plastic usage become stricter, the sector is positioned to adapt by accepting these sustainable methods, guaranteeing long-term viability and reducing dependence on non-renewable sources. The integration of sustainability into plastic shot molding is not simply a trend; it is coming to be a crucial part of business responsibility and functional quality.
Advancements in 3D Printing
Current improvements in 3D printing innovation are significantly changing the landscape of plastic injection molding. The integration of additive production processes permits for the fast prototyping of complex geometries that were as soon as difficult or difficult to achieve via conventional methods - Plastic Injection Molding. This ability not just accelerates item development cycles however additionally decreases product waste, aligning with the expanding need for sustainable production practices
Additionally, the appearance of crossbreed production techniques, which integrate 3D printing and shot molding, provides makers the ability to produce complex designs while maintaining the effectiveness of mass manufacturing. This method allows the web link manufacturing of customized parts tailored to certain consumer requirements without compromising the rate and scalability that shot molding gives.
Additionally, developments in products, such as high-performance polymers and compounds especially designed for 3D printing, are enhancing the practical abilities of published parts. These products can withstand greater tension and display enhanced thermal buildings, making them ideal for more demanding applications.
As 3D printing remains to evolve, its integration into plastic injection molding procedures assures to boost performance, reduce prices, and foster innovation in item layout, placing producers to much better meet the difficulties of a competitive market.
Data Analytics and IoT Integration
Data analytics and the integration of the Net of Points (IoT) are changing plastic shot molding by supplying makers with unmatched insights into their procedures. By leveraging real-time information gathered from interconnected devices and sensors, manufacturers can check efficiency metrics, determine inefficiencies, and optimize manufacturing processes. This data-driven method facilitates anticipating maintenance, reducing downtime and expanding tools life expectancy.
Furthermore, IoT assimilation enables enhanced quality assurance. By constantly tracking variables such as stress, cycle, and temperature times, manufacturers can promptly discover deviations from developed parameters and make changes in real time. This not just improves item consistency yet also minimizes waste and scrap rates.
The blend of data analytics and IoT innovations also equips suppliers to embrace even more agile production approaches. With access to thorough data analytics, organizations can reply to market demands with higher adaptability, adjusting production timetables and configurations as needed. This flexibility is essential in a quickly transforming production landscape.
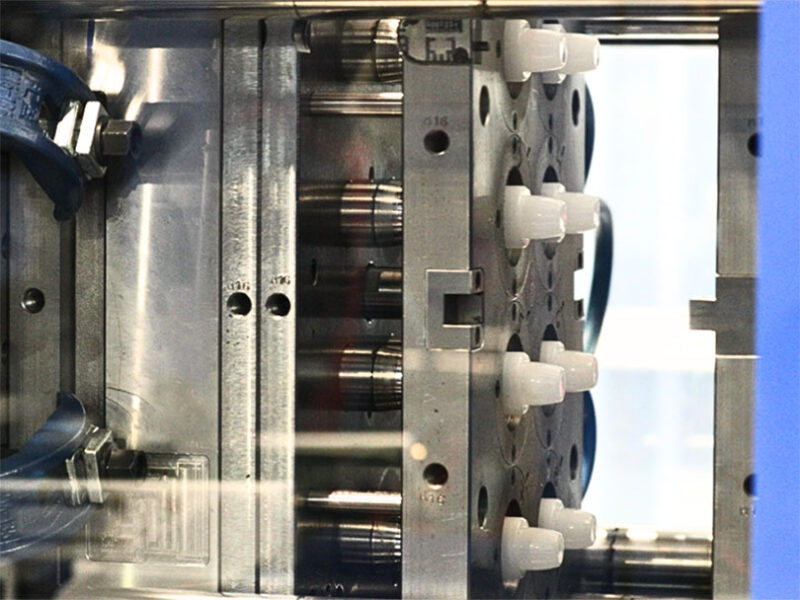
Customization and Layout Adaptability
Just how can personalization and design versatility enhance the competition of plastic injection molding? Customization enables producers to fulfill certain client requirements, accommodating one-of-a-kind dimensions, forms, and functionalities that standard products might not meet.
Advancements in style technologies, such as computer-aided style (CAD) and rapid prototyping, additional bolster this pattern. These devices allow developers to create complicated geometries and intricate patterns, which can be perfectly incorporated into the manufacturing procedure. Therefore, makers can react swiftly to transforming customer preferences and market needs.
Moreover, the application of modular tooling systems boosts design versatility, permitting quicker adjustments in between different item designs without considerable downtime. This adaptability can result in decreased preparations and reduced manufacturing costs, making business a lot more competitive and active. Inevitably, embracing customization and style versatility in plastic shot molding not just boosts item offerings but also strengthens find more market positioning in an ever-evolving landscape.
Final Thought
The future of plastic shot molding is defined by significant advancements in automation, lasting techniques, and ingenious materials. Modification via modular tooling and fast prototyping will make it possible for makers to stay competitive and receptive to the vibrant demands of the market.
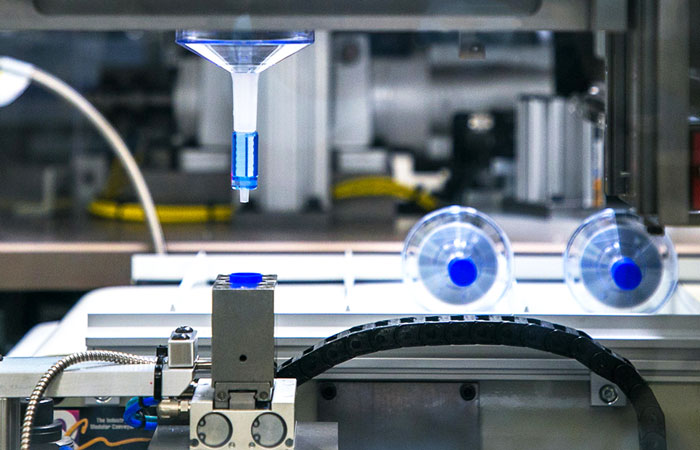
The future of plastic injection molding is defined by substantial innovations in automation, sustainable practices, and innovative materials.